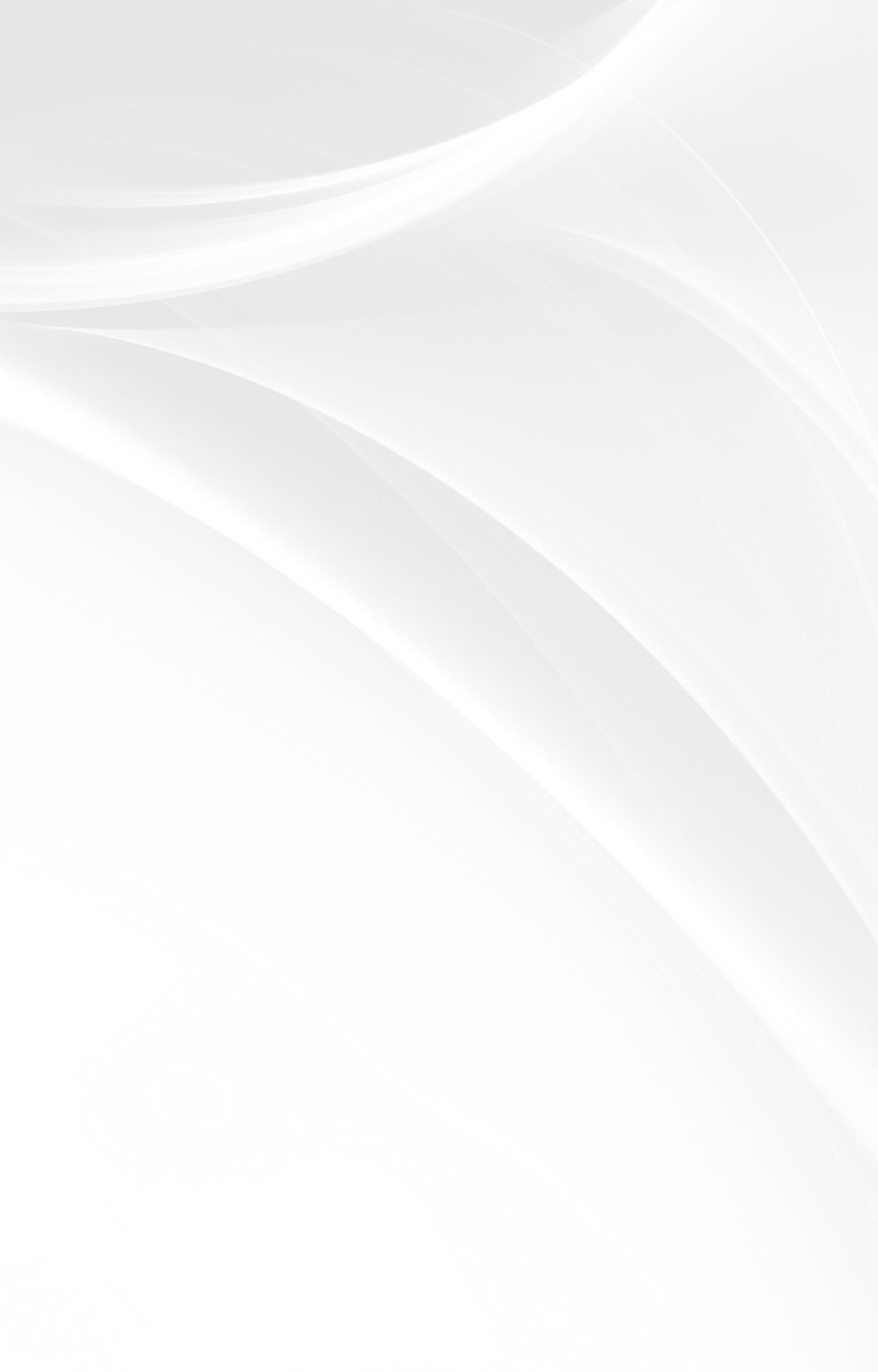
-
High Energy Centrifugal Barrel Finishing has been a method of heavy stock removal and deburring since the 1940's. UNITED's patented machines and processes rely on a commonly used method for polishing objects, which can be referred to as centrifugal force tumbling. In its most basic form, this approach consists of a Turret and four barrel which rotate at a high speed exceeding 300 RPM. At these speeds, G forces in excess of 25Gs can be generated inside the barrels. The centrifugal force pushes the work pieces and the media to the periphery of the barrels. Since the barrels are rotated in the opposite direction of the turret (similar to a Ferris wheel) at a 1:1 ratio, a slide is created within the barrel which causes the media to move across the work pieces and abrade the surface removing minute amounts of material at every rotation. Due to the high centrifugal force, the work pieces do not tumble, thus eliminating part-on-part impingement that other systems are prone to creating. By implementing extremely high gravitational forces upon the media mass, a high amount of aggression is exerted upon the part load, resulting in a drastically reduced cycle time in comparison to alternative methods of mass finishing. The system can completely automate the finishing process.
Centrifugal Barrel Finishing Systems are also referred to as: mass finishing systems, barrel finishing systems, tumble finishing systems, high energy systems, media finishing systems, deburring systems, ceramic finishing systems, Harperizers, among others.
-
By utilizing United's machines, manufacturers are able to finish parts in as little as 5 minutes, as opposed to a manual process which may take as long several hours or days. Eliminating the labor intensiveness allows manufacturers to complete finishing in their primary production facilities rather than suffer the inventory and logistical problems of shipping parts to and from deburring houses. The quality of finish is dramatically better with United's process; all surfaces are uniformly finished, including undulations, grooves, holes, and crevices. The entire part is exposed during the process, so the backs, sides, and bottoms are also deburred and polished. Unlike conventional manual processes, United's process primarily uses water and other non-toxic and biodegradable materials. All of this is done at a fraction of the cost of manual deburring or polishing.
-
The biggest drawback to early model CBF systems was the ability to harness the energy created within the barrel and reduce or eliminate part-on-part damage or impingement. The development of the CPC (Computerized Programmable Controller) by United has overcome these perils. The CPC is a PLC-controlled high energy centrifugal barrel machine with a touchscreen interface, process storage capabilities, and total G-Force control. By monitoring loading and process operations, the ability to achieve ultra-fine finishes on all materials while controlling impingement is a consistent and continuous reality, resulting in higher production rates, lower part costs, and reduced material costs. The CPC controls are only available through United. The CPC system makes the operation and maintenance of the machines simple. By localizing all of the controls to a single touchscreen, all the operational functions and information are a touch away, including prompts for maintenance and troubleshooting.
-
Item descriptionThese systems are ideal for lean manufacturing operations. The machines are portable enough and don't require any setup time to change processes.
If and when a project is complete, United's system can adapt to new projects within minutes.
-
United's systems, which come standard with PLC and touchscreen controls, prevent operator errors. All the parameters are programmed into the system prior to processing with digital lockout systems to prevent tempering by operator.
-
United offers free process development. Simply send your parts with the Parts Submission Form on our Contact page so we can test your parts in our machines before any purchase is made with no cost to you. We stand behind our products and wait for client approval of finished parts before proceeding to equipment sales.
-
United's customer base expands across the world and across all industries. United has been qualified to serve the aerospace industry, the military, the automotive industry, the aeronautical industry, the medical industry, the jewelry industry, and many others.
-
1. The only similarity between a vibratory, drag, vibrahone, tumbling, drum systems, and a CBF is that they both use abrasive media during processing. The following are some of the differences: Vibratory systems generate 1G of force vs. 25+ Gs generated by a CBF. This results in process cycles that are 20 times faster. This higher G-force also forces the abrasive (media) into tighter corners and holes that a vibratory machine cannot access because the media merely bounces off the part.
2. Vibratory systems work as the name sounds; they vibrate, causing the parts to bounce against one another thus causing part on part impingement. CBFs generate a sliding motion inside the barrels; even when parts come into contact with one another, they don't cause any damage.
3. The processes in vibratory systems cannot be controlled. In most cases, an operator will place parts in the bowls and periodically inspect a part to check for completeness. Unfortunately, the same process will yield a different result during the next cycle. A CBF, however, will achieve consistent results every time.
4. If you are looking to process soft material like aluminum and you are trying to achieve a flat surface or a finish with a high luster, a vibratory machine simply cannot deliver. A CBF will achieve a highly polished surface finish, which is why jewelers prefer CBFs.
5. Drag systems are somewhat similar to vibratory systems with one difference: As the name suggests, drag systems drag the parts through the media. The parts are affixed to a rotating arm on a center spindle that forces the part through the media. This method removes more material than vibratory machines, material removal is more on the edges of the parts.
-
Thanks to the CPC system, once a process has been developed and stored in the system you can expect above 99% accuracy and consistency.
Unlike manual deburring, all parameters of the process are controlled, eliminating the possibility of damage to parts.
-
Any material can be deburred, polished, or refined in a CBF including:
Titanium, Gold, Silver, Zinc, Aluminum, Brass, Steel, Stainless, Pewter, Beryllium, Barium, Cadmium, Vanadium, Copper, Nickel, Zirconium, Tungsten, Iron, Tin, Vasco x-2m,9310, M50, Vim-var, Bismuth, Palladium, Yttrium, Niobium, Magnesium, Manganese, Scandium, Osmium, Plastics, and Glass
-
None! We don't use any hazardous chemicals in our processes. The only components used in the process are:
Customer part, abrasive media, water, and detergent.
-
Due to the nature of the process, 0.000001 tolerances can be held through our CPC systems. No one else can make this claim.
-
Deburr: Most common use to remove all types of burrs after machining process. Remove sharp edges internally or externally.
De-scale: Optimal method of removing scale after heat treatment without the use of chemicals or media blasting.
Radius/Edge-break: Controlled edge-break without distortion. Achieve a perfect and consistent radius.
De-flash: Remove flash from all type of castings and injection molded parts including plastics and rubber.
Refine surface: Refine surfaces to .002 RA without any manual grinding or polishing.
Super-finish: Super blend surfaces after grinding process to take it to the next level.
Polishing: Parts can be polished to a high luster finish. Such as Gold and Silver jewelry.
Super Blend: Blend surface imperfections.
-
No. United's systems do not utilize any hazardous chemical products. Aside from your parts, only abrasive media, water, and a detergent are used in the process. The waste generated can easily be treated and recycled at minimal expense. Closed loop systems are also available.
See our Water Recycling Systems.
-
No, the consumables are much less expensive than those used in manual operations. There are only two types of consumables required to process parts: abrasive media, and detergents. These consumables can be purchased through United and in most cases they can be cross referenced and purchased from other manufacturers.
-
Yes, in most cases you can put several parts per barrel, depending on size and material. However, there are times when parts are not allowed to come into contact with another; in these situations, depending on type of equipment, parts can be segregated by using divided compartments available with our machines, or a type of fixturing device that will hold the parts in a fixed position.
-
Obviously it differs from one project to the next; however, most processes do not exceed 30 minutes. We at United understand that throughput is important, we strive to develop processes that minimize cycle times by experimenting with different medias to achieve the desired result in as little time as possible while keeping in mind the cost of the process. As, always we offer this process development to you at no charge.
-
Material handling varies for the different models. For the CPC6000 & CPC12000 the material handling is fully automated:
- Separator for media and parts. *Elevator to move media from separator to hopper.
- Rinse system to wash parts and media.
- Parts dispensing system.
- Media is loaded into barrels at a predetermined amount and reloaded back into hopper system when finished.
- Water is loaded into barrels at a predetermined amount. *Compound is loaded into barrels at a predetermined amount.
-
United's machines offer the most automated systems in the industry. Most of the automation comes standard with the machines and some can be included as options. Standard automation includes:
- Computerized process controls.
- PLC/touchscreen operation.
- Recipe storage.
- Material handling (not available on CPC250, CPC1000 and CPC2500)
- Media/parts separating system.
- Media/parts rinse system.
- Media, water, and compound loading.
- Barrel lid-lift (available on CPC6000 and CPC12000)
- Wastewater dispensing system. Specialized automation is available upon request.
-
Please refer to each machine’s page for specifications including electrical requirements, capacity, dimensions, and more.
-
Based on customer input over the last 10 years, the average ROI is 6 months. Implementing United's processes will virtually eliminate all manual work done to work pieces and all the problems associated with it. Rejection rate will decrease to almost 0%, and rework will be nonexistent.
-
Thanks to our patented components and our exclusive PLC/touchscreen operation, we can train an operator in less than an hour. We have eliminated the guess work from the machine settings and complicated manuals. We have eliminated all the tools that other types of machines require and replaced them with simple components that work seamlessly and without effort.
-
United’s machines are designed to ensure the safety of the operators and the longevity of the machines. Every single component on the machines is engineered and tested through finite element analysis where they were subjected to unrealistic forces to ensure against the unexpected. We have even sacrificed new machines with destructive tests; no other manufacturer takes these precautions. Our entire line of machines is UL and CE approved.
-
Minimal. All components are designed to last for decades. Aside from the occasional lubrication, not much else is required. At a preset frequency, based on hours of use, most models will prompt the operator that the machine is due for maintenance. The machine is designed so that the operator can access any part of the machine by removing no more than four bolts to remove a panel which will expose the whole side of the machine. Every component that requires maintenance is easily accessible.
-
Please refer to the specifications listed in each machine’s product page for maximum part dimensions.
-
All of United’s equipment is manufactured in California, USA.
-
Centrifugal barrel systems were first patented in 1904. However, United has filed and received several patents in the United States and over 25 other countries. As we continue to improve these systems; every new method is continuously submitted to the patent office.
-
Please refer to the quote document for the machine you are interested in. Most models come with up to a three-year limited warranty depending on the component.